당신은 주제를 찾고 있습니까 “사출 불량 종류 – #시험사출 #불량종류 #불량별 사출대처법 #사출 노하우 불량 유형별 대처 방법!!!“? 다음 카테고리의 웹사이트 th.taphoamini.com 에서 귀하의 모든 질문에 답변해 드립니다: https://th.taphoamini.com/wiki/. 바로 아래에서 답을 찾을 수 있습니다. 작성자 터프가이의생활 TV(Tough guy life TV.) 이(가) 작성한 기사에는 조회수 1,150회 및 좋아요 73개 개의 좋아요가 있습니다.
- 충전 부족 (Short Shot)
- 흑줄 (Black streak)
- 크랙 (Crack)
- 플래시 (Flash, Burr)
- 플로우 마크 (Flow Mark)
- 젯팅 (Jetting)
- 싱크 마크 (Sink Mark)
Table of Contents
사출 불량 종류 주제에 대한 동영상 보기
여기에서 이 주제에 대한 비디오를 시청하십시오. 주의 깊게 살펴보고 읽고 있는 내용에 대한 피드백을 제공하세요!
d여기에서 #시험사출 #불량종류 #불량별 사출대처법 #사출 노하우 불량 유형별 대처 방법!!! – 사출 불량 종류 주제에 대한 세부정보를 참조하세요
오랜만에 업로드하는 사출 관련 영상입니다~
불량 유형별 대처 방법! 많은 시청 부탁드립니다^^
문의사항 👇
[email protected]
https://band.us/band/83417581/post/2…
Music by : 브금대통령
♠ 카톡아이디 lsg3183
사출 불량 종류 주제에 대한 자세한 내용은 여기를 참조하세요.
금형사출 불량 사례 모음 – 크렐로
금형사출 불량 사례 모음 · 미성형(Short shot) · 플레쉬(Flash/Burr) · 싱크마크(Sink Mark) · 플로우마크(Flow Mark) · 실버 스트릭(Silver Streak) · Cloudy Surface (Gas자국).
Source: creallo.com
Date Published: 7/30/2022
View: 9464
사출성형(플라스틱가공)의 불량 원인과 대책
사출성형(플라스틱가공)의 불량 원인과 대책 · 1. 수분 및 휘발분. ▻ 충분한 건조를 한다. · 2. 수지의 분해 · 3. 공기의 흡입. · 4. 게이트가 작고 사출속도 …
Source: dotrazi.tistory.com
Date Published: 2/11/2022
View: 4255
사상 사출금형과 사출불량의 종류 – Daum 카페
사상 사출금형과 사출불량의 종류 · 1) 미성형(Short Fill) · 2) 표면수축(Sink) · 3)버어(Burr) · 4) 웰드 라인(Weld Line) · 5) 은조(Silver Streak) · 6) …
Source: m.cafe.daum.net
Date Published: 4/9/2021
View: 4614
품질 관리자가 알려주는 사출 성형 불량 원인 – FEAN diary
사출 성형 불량 원인 · 쇼트 (Short Shot) · 금형 상처, 긁힌 상처 (Mold Mark) · 플래시 (Flash) 또는 버 (Burr) · 싱크 마크 (Sink Mark) · 웰드 라인 (Weld …
Source: fean.tistory.com
Date Published: 6/19/2021
View: 6992
플라스틱 사출성형 조건 불량원인 및 대책 – 산비탈
1. 사출성형 설비의 종류 및 성형 공정. 수평 사출성형기. 사출성형 설비의 종류는 수평식 사출기에 직압식 …
Source: sanvital.tistory.com
Date Published: 1/16/2021
View: 7798
Top 10 사출 불량 종류 The 112 Correct Answer
사출 성형에 있어서 성형 불량의 원인은 크게 10가지 정도로 구분될 수 있습니다. 충전 부족 (Short Shot); 흑줄 (Black streak); 크랙 (Crack) …
Source: toplist.xosotanphat.com
Date Published: 4/8/2022
View: 578
사출성형 불량의 유형 및 대책-4 (웰드라인, 보이드, 싱크마크 …
사출성형 불량의 유형 및 대책-4 (웰드라인, 보이드, 싱크마크, 숏샷, 버) · 웰드 라인 · 보이드(공동) · 싱크마크 · 숏 샷 · 버(플래시), 오버 팩(과충전) …
Source: kjygamja.tistory.com
Date Published: 2/4/2022
View: 7905
사출 불량 유형 – 수축(Sink Mark) | TechBox
사출금형불량유형 – 수축(Sink Mark). 제품의 표면에 움푹 패여 보이는 부분을 수축(sink mark)이라고 한다. 싱크마크는 성형불량 현상 중 가장 발생 …
Source: techgoogleblogger.blogspot.com
Date Published: 11/29/2022
View: 9307
주제와 관련된 이미지 사출 불량 종류
주제와 관련된 더 많은 사진을 참조하십시오 #시험사출 #불량종류 #불량별 사출대처법 #사출 노하우 불량 유형별 대처 방법!!!. 댓글에서 더 많은 관련 이미지를 보거나 필요한 경우 더 많은 관련 기사를 볼 수 있습니다.
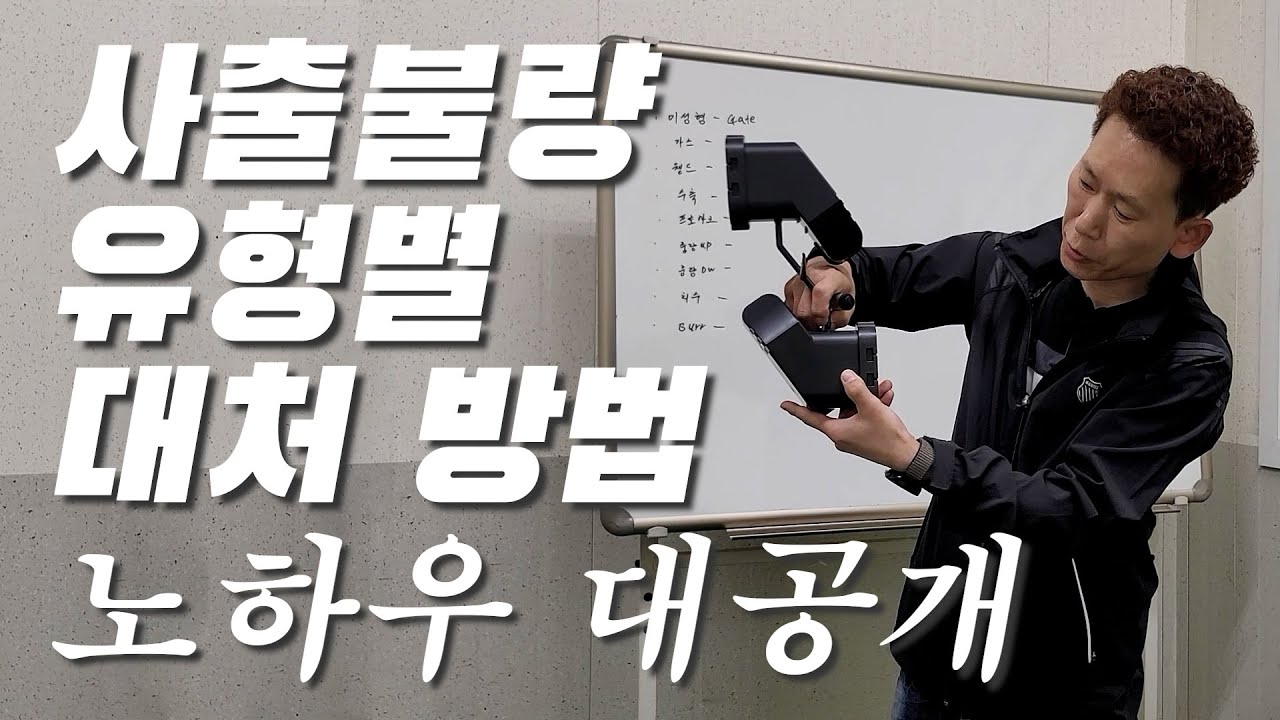
주제에 대한 기사 평가 사출 불량 종류
- Author: 터프가이의생활 TV(Tough guy life TV.)
- Views: 조회수 1,150회
- Likes: 좋아요 73개
- Date Published: 2022. 6. 12.
- Video Url link: https://www.youtube.com/watch?v=-6462ibQG3Y
사출성형에 있어서 성형불량의 원인과 대책
사출성형에 있어서 성형불량의 원인과 대책
사출 성형에 있어서 성형 불량의 원인은 크게 10가지 정도로 구분될 수 있습니다.
1. 충전 부족 (Short Shot)
2. 흑줄 (Black streak)
3. 크랙 (Crack)
4. 플래시 (Flash, Burr)
5. 플로우 마크 (Flow Mark)
6. 젯팅 (Jetting)
7. 싱크 마크 (Sink Mark)
8. 은줄 (Silver Streak)
9. 휨 / 변형 (Warpage)
10. 웰드 라인 (Weld Line)
다음 10가지의 불량의 원인과 대책에 대하여 포스팅 해보려 합니다.
1. 중전 부족 (Short Shot)
수지가 캐비티에 완전히 충전되지 않고 냉각 고화하는 현상
대책
1) 다수개폐기의 경우 일부가 충전 불량일때
: 게이트 밸런스 불량이므로 게이트 밸런스 보정
2) 수지의 유동성 부족
: 사출온도를 높이거나 사출압력 또는 속도를 높임, 유동성이 높은 수지 선정
3) 사출기 용량에 비해 금형이 큰경우
: 사출기 용량이 큰것으로 교체
4) 금형내 유동저항이 큰경우
: 유동저항을 크게 받는 부분의 직경을 증가시킴
5) 캐비티 내 공기가 빠지지 않음으로써 생기는 경우
: 사출속도를 낮춤으로써 공기가 빠져나갈 시간을 준다.
6) 호퍼에서의 수지 공급 부족
A) 호퍼부의 과열로 호퍼에 Pellet이 붙어 낙하하지 않음
: 호퍼부 온도를 낮추거나 냉각수를 사용, 호퍼부 온도를 떨어뜨린다.
B) 윤활성이 과다한 Pellet으로 스크류가 Pellet을 앞으로 보내지 못함
: 윤활성이 적은 Pellet 사용
2. 흑줄 (Black streak)
성형물에 흑갈색의 흐름 모양이 나타나는 현상
대책
1) 금형 표면에 기름등이 부탁되어 있는 경우
: 금형 표면에 기름, 그리이스가 묻어있거나 이젝터 편에서 기름, 그리이스 등이 나오는 경우로
금형 표면을 깨끗한 상태로 유지하도록 한다.
2) Hot-Runner의 색상 교체 불량인 경우
( Manifold 내에 체류 된 수지가 남아 있어 Gate 부근에 흑줄 발생)
: 기존 수지가 체류되지 않도록 MainFold의 구조변경
3) 수지의 열분해에 의한 경우
: 실린더 내의 체류시간을 적게 하거나 과열을 방지 수지온도를 내리고 사출속도를 느리게 한다.
때때로 퍼징을 하는 것도 좋다.
4) 호퍼 부근의 냉각의 불충분한 경우
(수지가 공급될 때 공기가 같이 들어가면 이 공기에 의해 수지가 타게 되어 발생)
: 호퍼부의 냉각수 양을 늘리고, 호퍼다음의 실린더 온도를 낮춘다.
5) 사출기 손상에 의한 경우
(실린더 배부나 역류방지 밸브 등이 타서 부서진 경우 발생)
: 이 경우 노즐의 조임 부분 등에서 탄 수지가 많이 나오므로 신속한 교체 필요
3. 크랙 (Crack)
성형물 표면에 금이 가는 현상
대책
1) 잔류응력에 의한 경우
: 캐비티 과충전에 의한 경우, 불균일한 살 두께에 의한 경우, 이형 시에 발생하는 경우 인서트 주위에 발생하는 경우, 금형온도 또는 수지 온도가 부적당한 경우
2) 외부 응력에 의한 경우
: 성형품 형상 불량에 의한 응력의 집중, 후 가공 시 외부응력에 의한 경우, 반복 / 진동 하중에 의한 경우, 열팽창 수축에 의한 경우
3) 환경 응력에 의한 경우
: 화학약품에 의한 경우, 열에 의한 경우, 자외선에 의한 경우
4) 금형의 빼기 구배 부족인 경우, 금형면의 연마불량
5)캐비티 과충전에 의한 경우
(가장 많은 압력이 걸리는 게이트 부근에 크랙 발생)
: 수지의 유동성을 높여 낮은 사출압력으로 성형, 실린더 온도를 높이거나 사출속도를 빠르게
한다.
6) 금형 온도가 부적절한 경우
: 금형 온도가 불균일한 경우 냉각차에 의한 응력이 발생한다.
7) 불균일한 제품 두께에 의한 경우
(두꺼운 부분의 냉각이 불충분한 상태에서 취출 시 이젝터 핀 주위에 발생)
: 충분한 냉각시간을 주거나 성형품의 두께가 면하는 부위에 R 또는 테이퍼 처리를 한다.
8) 사출조건에 의해 해결이 불가능한 경우 강도, 분자량이 높은 수지로 재료 변경 필요.
4. 플래시 (Flash, Burr)
금형의 파팅면 등의 틈에 수지가 흘러 정상 성형물보다 면적이 넓어지거나 중량이 늘어나는 것
대책
1) 금형 파팅면 불량에 의한 경우
: 금형 파팅 면의 보수 필요
2) 과도한 사출 압력과 사출속도
(냉각 시 압력이 가장 높은 게이트 부나 런너 부근에 발생)
: 사출 압력과 사출 속도를 낮춘다.
3) 형체압이 부족한 경우
(성형품 투영 면적에 비해 형체력이 작은 경우)
: 높은 형체력을 갖는 사출기로 교체 필요
4) 성형기의 보수 관리가 나쁜 경우
(유지 관리가 불량하면 형체력에 좌우, 상하 불균형이 생겨 발생)
: 주기적으로 성형기 점검이 필요
5. 플로우 마크 (Flow Mark)
대책
1) 게이트 부가 필요이상으로 냉각되는 경우 (수지 온도 저하가 현저해 지고 고점도가 된다.) : 금형 파팅면의 보수 필요 2) 수지 점도가 높은 경우 (수지 점도가 너무 높으면 충분한 사출압력을 전달 할 수 없다.) : 수지 온도와 금형 온도를 높이고 사출 속도를 빠르게 함으로써 수지 점도의 증가를 막는다. 3) 금형 온도가 낮은 경우 (수지, 냉각이 빠르게 일어나 수지 점도가 급격히 증가한다.) : 금형 온도 제어기를 이용하여 적절한 온도로 금형 온도를 유지한다. 4) 사출 속도가 느린경우 (캐비티 충진 속도가 늦어진다.) : 금형온도, 수지온도를 높여서 늦은 사출 속도로 인하여 충진 도종 수지가 빼앗기는 열량을 보충한다.
6. 젯팅 (Jetting)
성형물 표면에 케이트로 부터 리본 모양의 흐름자국
대책
1) 게이트 구조불량 (게이트가 작거나 얇은 부분에서 사출된 수지의 유속이 갑자기 빨라져 발생) : 게이트의 단면적을 넓힌다. 게이트 단면적 X 유속 = 사출량 게이트의 가로와 세로비는 1:3~1:2가 적당하다 2) 콜드 슬러그 웰이 작거나 없는 경우 (노즐 통과 시 냉각된 수지가 런너에서 다시 냉각되어 캐비티에 사출되어 그대로 냉각되며 발생) : 콜드 슬러그 웰을 만들거나 너무 작은 경우 크기를 크게한다. 3) 금형 온도가 낮은 경우 (금형 내에서 수지가 급냉되어 발생) : 금형온도는 사용 수지의 열변형 온도보다 20℃ 정도 낮은 온도가 적당하다. 4) 수지점도가 높은 경우 (수지 점도에 비해 사출온도가 낮은 경우) : 노즐 부분의 온도를 높인다.
7. 싱크 마크 (Sink Mark)
제품의 두꺼운 부분이나 리브(Rib), 보스(Boss) 등의 외츠면이 불충분한 냉각에 의해 안쪽으로 빨려
들어오는 현상
대책
1) 스프루, 런너, 게이트가 작은경우 (냉각 고화가 빨리 일어나 압력강하가 커지고 캐비티 내에 압력을 충분히 전달 할 수 없다.) : 압력 전달이 충분히 될 수 있도록 케이트, 런너의 크기를 크게 한다. 2) 금형 온도가 부적절한 경우 (성형품의 두께가 두꺼운 부분이나 리브 부분은 다른 부분에 비해 냉각이 늦으므로 안으로 함몰됨) : 리브 부분이 충분히 냉각될 수 있도록 구조를 조절한다. 3) 사출조건상의 원인 A) 사출압이 낮은 경우 : 사출압을 증가시킨다. B) 사출압 유지 시간이 짧은 경우 : 수지의 열 수축이나 역류가 일어나지 않도록 보압 유지 시간을 길게 한다. C) 쿠션량이 부적절한 경우 : 쿠션량이 너무 적으면 압력이 전달되지 않으며, 너무 많은 경우에는 압력이 실린더 전부에 있는 수지에 흡수되어 버리므로 적절한 양을 유지한다. (3 ~ 5 mm)
8. 은줄 (Silver Streak)
재료의 유동방향으로 은백색의 줄이 생기는 현상
대책 1) 게이트 구조불량 (게이트가 작거나 얇은 부분에서 사출된 수지의 유속이 갑자기 빨라지고 압력이 높아져 수지가 분해를 일으키며 발생) : 엔지니어링 플라스틱의 주요 발생원인 게이트의 단면적을 넓힌다. 2) 금형 표면 불량 (표면의 수분, 유분, 이형제 등이 용융수지 열에 의해 증발하여 가스가 되어 성형품에 발생) : 금형 표면을 알코올, 용제 등으로 청소 3) 사출압이 높거나 속도가 빠른 경우 (급격한 살 두께의 변화가 있을 때 유동 중 압축된 수지가 급격히 감압되어 팽창하면서 휘발분이 가스화 되었다가 금형면과 접촉 시 액화 되면서 발생) : 사출압을 낮추고 속도를 느리게 하여 휘발 가스가 충분히 배기 되도록 한다 4) 수지온도, 금형온도가 너무 낮은 경우 (수지의 냉각 고화가 빨라서 배기가 불충분하기 때문에 발생 : 수지와 금형 온도를 높여 냉각 고화를 느리게 한다 5) 수지의 열분해에 의한 경우 (수지 자체 또는 안정제,안료 등 첨가제가 분해되어 발생) : 불균일한 가소화나 체류에 의해 발생하므로 성형기 최대사출용량의 30 ~ 60% 범위에서 조작되도록 한다 6) 스크류 내에 공기가 혼입된 경우 : 배압이 없는 경우 혼입되기 쉽다 호퍼 하부의 냉각을 충분히 하고 실린더 후부 온도와 스크류 회전 수를 내린다 SUCK BACK 양을 줄인다 7) 수지의 수분 및 휘발분에 의한 경우 : 성형 전 충분한 건조로 수분이나 휘발분 제거 장마 때와 같이 공기 중에 수분이 높은 경우 호퍼에 수분이 맺혀 발생하기 쉽다 8) 재생 수지 사용에 의한 경우 (불균일한 형태의 재료가 혼입될 때 재료 사이의 공극으로 공기가 혼입) : 재생 수지를 사용할 경우 입자 크기를 균일하게 한다
9. 휨 / 변형 (Warpage)
대책 1) 냉각이 불균일한 경우 (성형품 부분간 냉각속도가 다를 때 발생 빨리 냉각되는 곳은 수축이 작고 늦게 냉각되는 곳은 수축이 크므로 발생) : 같은 속도로 냉각이 되도록 냉각라인 설치 게이트에서 멀 수록 수지온도가 낮아지므로 냉각 라인은 게이트 부근에서 먼 곳으로 향하게 한다 2) 부적절한 게이트 (게이트 위치가 부적절하여 캐비티 내의 충전시간에 차이가 큰 경우) : 게이트 위치 변경 먼저 충전된 부분과 나중에 충전된 부분의 수축율이 틀려서 발생
10. 웰드 라인 (Weld Line)
캐비티내에서 2개 이상의 분류된 흐름이 다시 합류할 때완전히 융합되지 않고 실모양의 가는 선으로
나타나는 현상
대책
사출성형(플라스틱가공)의 불량 원인과 대책
사출성형품의 불량원인과 대책
1. 성형제품의 불량
2. 성형제품설계 불량.
3. 금형설계 불량.
4. 금형가공 제작 불량.
5. 성형기계 불량.
6. 성형기계운전 조건 불량.
7. 원료수지 선택 불량.
8. 원료수지 처리, 첨가제 등의 불량.
Burr 불량
금형고정측과 가동측사이,슬라이드부분,insert의 틈새, 밀핀의 간격등에 수지가 들어가 제품에 필요이상의 지느러미가 생기는 현상.
주원인과 대책:
① 금형의 맞춤면, 분할면 등의 불량.
► 4개 또는 2개의 타이바를 균등하게 조정.
► 슬라이드 코아의 밀어젖힘력을 충분하게 한다.
► 좌우 분할금형은 사출압력에 견딜 수 있는 투영면적을 준다.
② 형체력 부족에 의함.
► 사출압력을 낮추거나 형체력을 높인다.
③ 수지의 점도가 낮음.
► 사출속도를 낮추거나, 금형의 온도를 낮춰서 점도를 저하시킨다.
► 캐비티 용적에 비해 수지 공급량이 과다 하지 않도록 주의한다.
④ 금형 사이에 이물이 끼어 있음.
수축불량(sink mark)
성형품 표면에 움푹 파인 현상.
주 원인과 대책 :
① 사출압력이나 보압이 부족하여 발생되는 수축.
► burr가 발생되지 않는 범위 내에서 사출압력을 높여주고 보압 시간을 길게 한다.
② 충분한 사출압력에도 발생되는 수축.
► 스프루나 런너,게이트의 직경이 작은지 검토한다. ③ 금형냉각량이 부족하거나 금형온도 불 균일. ► 냉각수 온도나 구조상 문제가 있는지 확인한다.
► 수축이 심한 boss나 rib부위는 냉동기를 활용하여 차가운 냉각수가 흐르게 한다.
④ 성형품의 살 두께 불 균일.
► 설계시 살 두께가 균일하게 해주고 불균일한 곳은 살 빼기, 살 붙이기를 해준다.
⑤ 살 두께가 너무 얇거나 게이트에서 멀 경우 발생. ► 게이트에서 멀면 수지가 흐르는 도중에 식어버려 수축이 발생된다. 스프루,런너, 게이트를 크게 하고 금형온도를 높인다.
은줄(Silver streak)
수지흐름 방향으로 은색, 백색의 자국이 흩어지듯 생기는 현상.
주 원인과 대책 :
1. 수분 및 휘발분
► 충분한 건조를 한다.
2. 수지의 분해
► 정전기 방지제나 난연제, 방청제등의 첨가제로 인해 생기기 쉽다.
► 수지가 분해하지 않도록 수지온도를 내리고, 실린도내에 체류시간을 짧게 한다.
3. 공기의 흡입.
► 수지가 들어갈 때 공기가 함께 들어가 생김.
4. 게이트가 작고 사출속도가 빠르면 발생.
► 사출 속도를 줄이고 게이트를 크게 한다.
5. 스크류 마찰열에 의한 발생
► 스크류 회전수가 너무 빠르지 않게 주의
6. 수지온도 저하
► 수지온도가 너무 높으면 가스를 빼 내지 못함.
7. 가스가 빠지지 않아서.
► 에어밴트를 설치해준다.
8. 금형온도가 낮을 때.
► 수지의 흐름이 차단되면 은줄이 생긴다.
미성형(Short shot)
설계로 목적했던 제품의 형상이 나오지 않는 현상.
주 원인과 대책 :
1. 성형기계의 능력 부족.
► 공급능력이 부족한 기계의 경우 발생.
2. 성형재료.
► 첨가제를 넣은 재료는 유동성이 나빠 나올 수 있다.
(가열실린더 온도를 높이고 압력을 높여 작업한다.)
3. 수지온도가 일정기준보다 낮을 때.
► 가열실린더 온도를 높이고 압력을 높인다.
► 금형의 온도를 높인다.
4. 리브나 보스에 발생.
► 가능한 분할 코어를 이용하여 가스를 제거해줌.
5. 금형 파팅 라인이 가스벤트 역할을 못함.
► 파팅면의 이물을 수시로 제거해줌.
6. 캐비티가 두 개 이상인데 일부가 미성형.
► 게이트밸런스와 성형품의 살 두께가 맞지 않음.
웰드라인(Weld line)
수지가 합류하는 부분에 가느다란 실선이 생기는 현상.
주 원인과 대책 :
1. 게이트가 여러 개소에 있다.
► 게이트 수를 줄이거나 위치를 옮기고, 사출압력과 속도를 조절한다.
2. 게이트와 상관없는 부분에 생김
► 살 두께에 편차가 있는 경우에 생기며 얇은 부분은 살 붙이기를 해 준다.
3. 공기 또는 휘발분의 유입.
► 에어밴트를 설치해준다.
4. 수지온도가 낮을 경우.
► 수지온도를 높여주어 수지가 합류할 때 융합하게 한다.
5. 금형온도가 낮을 때
► 온도를 높여 수지가 잘 융합하게 한다.
6. 사출압력, 보압 시간이 적을 때.
► 압력을 높이고 보압 시간을 길게 하면 앞단부에서 고화되는 것을 막을 수 있다.
7. 건조가 충분치 않은 경우 발생 할 수 있으므로 충분히 건조한다.
8. 설비 개선을 통한 대책
1) 유도전열장치
► 웰드가 발생하는 곳에 유도전열장치를 설치하여 순간적인 온도를 급상승하여 웰드를 없애는 방법.
2) 로직 시일 방식
► 로직 시일 방식
강제가스 빼기 장치를 활용하는 방법으로 냉각회로를 이용하여 공기를 흡입하는 방식.
3) 급냉, 급열 온도 조절방식.
► 사출시 금형온도를 고온으로 하고 완료시 금형을 순간적으로 급랭하는 방식.
휨(warp),굽힘(Bending),뒤틀림(Twisting)
수지흐름에 따라 휨이나 변형불량이 생김.
주 원인과 대책 :
1. 금형온도가 낮은 쪽으로 휨이 발생.
► 온도를 균일하게 하던지, 낮은쪽을 높여준다.
2. 금형온도가 부분적으로 다르다.
► 금형 냉각회로를 점검한다.
3. 사출압력이 너무 높거나 낮으면 발생.
► 압력이 높으면 열팽창에 의해 생김.
►낮으면 융합이 약해 휨이 발생할 수 있다.
4. 냉각이 충분히 안됨.
► 밀핀의 힘으로 휨이 발생할 수 있으므로 냉각을 충분히 해주던지 밀핀을 고루 분포시킨다.
5. 수지의 유동성이 나쁘다.
► 수지의 흐름방향의 수축률이 직각방향으로 흐르는 수축률보다 클 경우 발생.(리브를 설치하는 등 설계의 일부를 변경한다.)
6. 잔류응력에 의함 휨.
► 어니링을 실시한다.
7. 설계에 의한 휨 발생
► 살 두께를 균일하게 해준다.
►리브를 설치하여 휨을 방지한다.
치수불량
성형조건의 변화, 계절변화, 밤과 낮의 기온차, 성형재료의 Lot 변화, 설계시의 살 두께 편차, 금형제작시의 정밀도 부족등이 있다.
주 원인과 대책 :
1. 사출압력과 속도가 너무 높거나 낮다.
► 너무 높으면 치수초과나 burr가 발생되며, 너무 낮으면 치수미달이나 미성형, 수축불량이 나온다.
2. 금형온도
► 금형온도를 일정하게 유지시킨다.
3. 냉각시간이 짧음.
► 응력회복이 커지고 성형품의 밀도가 높아지므로 수축이 생김.
4. 환경에 의한 치수변화
► 계절, 밤과 낮에 따라 치수가 변할 수 있으므로 공장은 항상 일정한 온도와 습도를 유지하게 한다.
5. 형체력에 의한 불량.
► 형체력이 너무 높을 경우 가스가 빠지지 못해 치수가 작아진다.
흑점 및 흑줄 발생
공기가 압축과 고온으로 인한 열로 수지가 타는 현상.
주 원인과 대책 :
1. 성형재료에 의한 발생
► 난연제를 첨가한 성형재료는 수지온도를 최소화하여 가열 실린더 온도를 설정한다.
► 수지를 이물이 첨부되지 않도록 주의 보관한다.
► 실린더 내에 잔량을 최소화 한다.
2. 성형조건에 의한 불량
► 가열실린더 온도를 필요이상 높게 하지 않는다.
► 스크류회전수와 사출속도를 빠르게 하여 마찰열을 상승시키지 않는다.
► 호퍼 밑 부분이 냉각이 제대로 되지 않으면 탄화현상이 생긴다.
3. 사출성형기에 의한 불량
►실린더와 스크류 사이가 벌어져 수지가 조금씩 나오면서 불량이 발생된다.
► 노즐과 실린더 간에 벌어지면 틈 부위네 체류되어 있던 수지가 탄화되어 불량이 생긴다.
►실린더를 세척한다.
플로우 마크(Flow mark)
게이트 중심으로 반달 혹은 띠를 형성한 모양.
금형 내에 최초로 유입되는 수지의 냉각이 너무 빠르기 때문에 다음에 흘러 들어오는 수지와의 사이에 경계가 생겨 발생한다.
주 원인과 대책 :
1. 성형재료에 의한 플로우 마크
► 예비 건조를 한다.
► 실린더와 금형온도를 높여 유동을 좋게 한다.
2. 성형조건에 의한 불량.
► 사출속도를 높이거나 낮게 하여 마찰열을 조절한다.
► 사출압력을 높이고 보압 시간을 다소 길게 한다.
3. 설계에 의한 불량 대책
► 살 두께 변화를 완만히 하여 흐름을 좋게 한다.
► 에어벤트를 설치하여 가스빼기를 한다.
► 게이트부에 콜드 슬러그 엔을 설치한다.
젯팅 불량
사이드게이트와 오버랩게이트에 많이 생기며 수지가 끈 모양의 형태로 고화해서 성형품의 표면에 꾸불꾸불한 모양을 나타내는 현상.
주 원인과 대책 :
1. 유입되는 수지의 유속이 너무 빠르거나 유로가 길면 생기기 쉽다.
2. 차가운 수지가 금형내부를 통과한 후, 나중에 들어오는 뜨거운 수지가 흐를 때 표면으로 자국을 남김.
► 게이트를 재료의 두께방향으로 캐비티의 벽 근거리에 설치한다.
► 수지가 고화 되지 않도록 수지의 온도를 높인다.
► 콜드 슬러그웰을 설치하여 앞단부에 차가운 수지가 들어가지 않도록 한다.
► 게이트를 크게 한다.
크랙, 백화
크랙 : 성형품의 한 부분이 깨지거나 금이 가는 현상.
백화 : 깨지면서 발생되는 흰 부분, 또는 밀핀의 힘에 의해 억지로 빠질 때 자국으로 남는 현상.
주 원인과 대책 :
1. 사출압력에 의한 불량.
► 과 충전되면 내부응력이 발생되어 크랙이 발생되기 쉽다.
2. 잔류응력
► 사출 압을 너무 높이면 잔류응력이 발생될 수 있다.
3. 이형불량
► 충분한 빼기 구배를 준다.
4. 냉각 불충분에 의한 불량.
► 고화가 덜 된 상태에서 밀핀 주위가 깨지거나 백화가 발생할 수 있다.
5. Insert 주위가 깨지는 현상.
► 인서트는 수축하지 않고 수지만 수축하는 상태에서 응력이 집중 될 수가 있다.
제품개발,제품설계, 중국금형은 엑스코어에서! http://www.thexcore.com
사상 사출금형과 사출불량의 종류
사상이란-
금형에서 빼낸 제품에 붙어있는 불필요한 부분(burr 혹은 바리라고 불림)을 손질하는 마무리 작업
밀링, 연마 작업이 포함된다. 그라인더로 매끈하게 갈아내는 작업이라고 보면 됨.
사출금형의 종류 –
프레스금형(전단가공, 벤딩가공, 드로잉가공, 압축가공,연속가공)
단조금형(해머단조,프레스,오프세팅)
플라스틱 사출금형(사출,압축,이송,압출,블로우,진공,발포 등)
AL 다이캐스팅 금형(고압,저압,스퀴즈 등)
주조금형(사형주조,인베스트먼트,로스트왁스,셀주조,중력 등)
분말야금 금형(편입,양입 등)
요업금형(일반도자기,연삭 숫돌,타일제조,콘크리트 블록 등)
고무금형(압축,사출,압출 등)
유리금형(블로우,프레스&원심,프레스 등)
금형의 개념 –
학문적 개념 : 재료가 갖는 소성, 전연성, 유동성 등을 이용한 성형 가공으로 원하는 제품을 얻기 위해 만든 금속재료 소재의 틀
기술적 개념 : 동일규격의 제품을 대량으로 생산하기 위해 모든 모체가 되는 틀
사출 불량의 종류 –
1) 미성형(Short Fill)
사출량 부족, 가소화(계량)조건 부적합
사출압력,사출속도,보압부족 및 금형온도 낮음
제품 두께의 불균일 및 금형내 가스벤트 미흡
원재료의 유동성 부족
2) 표면수축(Sink)
보압부족, 또는 게이트 크기 작음
제품 살두께 두꺼움
제품 말단부에 보스(BOSS)나 립(RIB) 위치함
3)버어(Burr)
합형면 맞춤상태 부적합, 또는 형체력 부족
사출압, 사출속도 및 보압 과도하게 높음
금형온도 높음
원재료 예비건조 미흡
4) 웰드 라인(Weld Line)
제품 형상 중 구멍이나 유동방해형상 존재
게이트 수량 복수 개
원재료 예비건조 미흡, 또는 가스벤트 미흡
원재료의 유동성 부족, 또는 금형온도 낮음
웰드라인 정의 –
서로 떨어져 있는 유동 선단이 반대 방향에서 이동하다가 서로 만날 때 형성되는 부분을 통틀어 웰드라인이라고 합니다. 다시말해서, 두 개의 합쳐지는 유동 선단이 평행하게 흐르면서 그들 사이에 결합이 일어날 때 형성됩니다. 웰드라인은 게이트의 위치와 크기를 조정함으로써 낮은 응력(low-stress)이 발생하는 곳과 잘 안 보이는 곳(low-visibility)에 위치해야 합니다. 대게 웰드라인의 강도는 타 부분 대비 현격히 감소되는데, 이는 그 곳의 국부적인 온도와 압력을 증가시킴으로써 향상시킬 수 있습니다
가스벤트의 정의 –
용융 수지를 충진할 때 캐비티 안의 공기와 수지의 휘발 가스 를 형 밖으로 배출해야 하느데 이 배출 홈을 에어 벤트 또는 배기 구멍 이라 한다
5) 은조(Silver Streak)
원재료의 예비건조 미흡
가소화(계량)조건 부적합
제품 형상 중의 립(RIB)과 수지유동방향 동일
제품말단의 가스 벤트 미흡
체크링, 스크루 마멸
6) 가스탄화, 흑점(Burning , Black Streak)
원재료 예비건조 미흡
금형내 가스 벤트 미흡
제품 살두께 불균일에 의한 air-trap
스크루, 실린더헤드 및 청소 미흡
금형 슬라이드 코어 등의 구조부적합
7) 변형, 뒤틀림(Warpage)
제품두께 불균일 또는 냉각공 배치 불균일
원재료의 유동방향과 직각방향의 수축률차 큼
금형온도 너무 낮음
사출속도 느리고 보압 과대
에젝터 장치의 작동 불균형
8) 플로우 마크(Flow Mark)
게이트 크기 과소 및 사출속도 낮음
게이트 위치 부적합
금형온도 낮음
품질 관리자가 알려주는 사출 성형 불량 원인
반응형
품질 관리 업무를 사출이나 프레스 관련 업체에서 하고 있다면, 사출 성형 불량 원인을 꼭 숙지해야 한다. 그래야 업무를 능숙하게 이끌어 갈 수 있다. 품질 관리 업무를 하면서 제대로 된 성형 불량 원인도 모르고 무조건 NG 처리하여 반품하는 경우도 많다.
기구 설계나 금형 설계 구조에 따라 문제가 발생하는 경우도 있다. 따라서 품질 관리자는 사출 성형 불량의 원인을 알고 그에 따른 합리적인 대책을 제시해야 한다. 이번 포스팅은 품질 관리자가 꼭 알아야 하는 사출 성형 불량 원인을 정리하였다.
사출 성형 불량 원인
쇼트 (Short Shot)
성형할 수지가 충분히 가열되지 않거나, 사출 압력 및 금형 온도가 매우 낮을 경우, 금형 전체에 수지가 들어가지 않고 냉각 고화해서 성형품 일부가 모자란 현상이다.
금형 상처, 긁힌 상처 (Mold Mark)
금형 상처는 금형 표면의 상처가 제품 표면에 나타나는 현상이다. 금형을 수정하면 고칠 수 있다. 긁힌 상처는 금형의 역테이퍼 또는 테이퍼 부족으로 제품과 금형 마찰면에 생기는 상처이다. 수리하지 않으면 계속 상처가 발생한다.
플래시 (Flash) 또는 버 (Burr)
금형의 맞춤면 주로 파팅라인 (Parting Line)에서 자주 생긴다. 즉, 고정형과 이동형의 사이, 슬라이드 부분, insert 틈새, ejector 핀 간격 틈새, gas vent 주위 등에 수지가 흘러들어 가 필요 이상의 지느러미가 생긴 현상이다.
플래시 (Flash) 또는 버 (Burr)는 한번 발생하면 이후에 나오는 제품들은 더 큰 플래시가 생기게 된다. 금형을 오목하게 만들어 플래시가 더 커지므로 처음부터 발생하지 않도록 해야 하며, 플래시가 발생하면 금형을 수정한다.
주로 금형 맞춤면, 분할면 등 불량, 형체력 부족, 수지 용융 점도가 낮음, 금형 사이에 이물 등을 원인으로 꼽을 수 있다.
싱크 마크 (Sink Mark)
싱크 마크는 성형품에 있는 함몰된 부분을 말한다. 가장 많이 일어나는 성형 불량이다. 보통 수지의 성형 수축에 의해 발생하여 제거하기 어려운 부분이 있다.
사출성형은 냉각된 금형 용융 수지를 주입할 때 금형에 접촉한 면부터 냉각되고, 수지는 열전도가 나빠지고 매우 복잡한 현상이 생긴다. 금형에 접하는 표면이 빨리 냉각되어 고화, 수축하고 내부는 냉각이 늦으므로 수축도 늦는다. 빨리 수축하는 쪽으로 재료는 움직이고, 늦게 수축하는 부분은 수지량이 부족해서 기포가 된다.
싱크 마크는 성형품의 냉각이 비교적 늦은 부분으로 표면이 내부의 기포발생을 없애는 방향으로 끌려서 오목면이 되는 현상이다. 즉 성형품의 두꺼운 부분에서 발생하기 쉽다.
수축이 큰 수지에 심하다 : 폴리프로필렌, 폴리에틸렌, 폴리아세탈 등
성형품의 살 두께가 불균일하다.
금형의 냉각이 불균일하거나 불충분하다.
금형 내 압력이 부족해서 충분히 압축되지 않는다.
사출 속도가 너무 빠르다.
재료의 수축이 큰 것 등이다.
웰드 라인 (Weld Line ; Weld Mark)
웰드 라인은 용융 수지가 금형 내를 분기해서 흐르다가 합류한 부분에서 생기는 가는 선을 의미한다. 성형 시 구멍이 있거나 insert가 있을 때 발생한다. 웰드 라인은 2개의 게이트로 성형할 때도 발생하는데 게이트 위치를 변경하여 웰드 라인을 눈에 잘 보이지 않게 위치를 바꾸는 것 이외에 다른 방법은 없다.
웰드 라인은 분기해서 흐른 용융 수지의 앞쪽 부분이 다시 합류할 때까지 냉각되어 완전히 융합하기 어려워 합류하는 곳에 줄이 발생한다. 웰드 부분은 융합이 완전하지 않아 강도 저하가 발생하므로 반드시 고려해야 할 부분이다.
플로우 마크 (Flow Mark)
플로우 마크는 수지가 흐른 자국이 나타나는 것이다. 형태는 게이트 중심으로 동심원의 얼룩무늬, 광택, 표면 거칠어짐이 발생한다.
원인은 금형에 처음 유입한 수지의 냉각이 너무 빠르기 때문에 다음에 흘러 들어오는 수지와의 사이에 경계가 발생한다. 이는 수지의 정도가 지나치게 높고 수지 온도와 금형 온도가 불균일하거나 성형품의 살 두께 변화가 많고 단차가 급한 것에 발생하기 쉽다.
광택불량(표면흐림)과 가스자국
광택 불량과 가스 얼룩은 성형품의 표면이 원래 광택과 다르고 유백색의 막이 덮여 안개 낀 듯한 상태가 되는 현상을 의미한다. 원인은 금형 표면에 수지가 충분히 밀착하지 못하고, 가스가 금형 표면에 응축해서 금형면에 접착을 방해한다. 그 외 금형의 연마 부족, 윤활제, 이형제 과다 도포도 원인이다.
– 자료 출처 : 최신 제품 설계 [이국환]
– 이미지 출처 : 네이버 사출금형/성형기술 카페, 작성자 미카엘(caild77)
반응형
플라스틱 사출성형 조건 불량원인 및 대책
플라스틱 사출성형 조건 사출 불량원인 및 대책
사출 성형이란 플라스틱(RESIN)에 열을 가하여 가소화 시킨후 유압으로 용융수지를 금형에 주입하여 원하는 형상의 제품을 만들어 내는 것을 말합니다.
사출성형에는 여러 설비들을 필요로 하지만 그 중에서 사출성형기,금형,사용재료 가 가장 중요하며 설비,금형,원료의 특성들을 잘 조화시켰을 때 사출성형이 가능하게 되며 목적에 부합하는 양질의 제품을 생산할 수 있을 것입니다.
사출성형은 1872년 금혀에 처음 사용한 것으로 시작하여 현재는 사출 성형기에서 플라스틱 수지,열경화성 수지,열 가소성 수지를 용융시켜 금형의 틀 안으로 주입하여 용융수지를 고화시켜 만드는 것입니다.
1. 사출성형 설비의 종류 및 성형 공정
수평 사출성형기
사출성형 설비의 종류는 수평식 사출기 에 직압식,터글식,전동식 등으로 분류하고 수직식(다대사출기) 등 주로 사용하는 방식의 4종류로 구분합니다
사출성형공정
사출성형 공정 은 형폐,노즐텃치,사출,보압,냉각,계량,형개,취출공정 등으로 1 Cycle이 이루어집니다.
사출성형 요소는 설비(사출기),금형,레진,사람,사출조건 등의 주요소와 주변 설비인 쿨링타워(냉각수),온도조절기(온수기,온유기),칠러,핫트런너콘트롤러,타이머,호이스트 등 보조적인 주변설비가 있습니다.
2. 사출성형 조건 구성요소
사출성형 조건의 구성요소를 보면 성형조건은 크게 주조건과 보조조건으로 구분하며 주조건은 성형조건에 주가 되는 조건을 말하며 보조조건은 주조건의 보조 역할을 하며 주 조건이 제 기능을 할 수 있도록 도와주는 역할입니다
주조건이나 보조조건 모두 플라스틱 사출성형에 있어 매우 종요한 요소입니다.
사출성형조건
양질의 부품을 생산하기 위한 사출성형 조건은 성형재료,사출성형기,금형,성형기술자 등 다양한 요소가 영향을 미치며 이에 대한 몇가지 요소들을 정리하도록 하겠습니다
사출성형조건
(1) 사출 성형온도
사출 성형온도는 사출성형 전반에 걸쳐 제품의 완성도를 좌우 한다고 해도 과언이 아닙니다.
설비,금형,냉각수,수지 등 모든 인풋 요소들의 성형온도가 해당 제품이 필요로 하는 조건에 적절히 설정되어 있지 않으면 다른 조검이 아무리 적정하다고 하여도 Loss만 증가할 것이니 성형온도 설정은 사출성형에 있어 키포인트라 할 수 있습니다.
예를들어 PC 수지의 경우 실린더 온도설정을 250℃ 이상으로 설정 하여야 하는데 250℃ 이하로 온도를 설정하면 수지가 녹지 않아 계량시 사출 스크류에서 소음이ㅣ 발생하며 스크류가 파손되든가 설비가 고장을 일으키게 될 것입니다.
(2) 흐름방지 (Suck Back)
사출성형 조건의 흐름방지(Suck BacK)란 용융수지의 흘러내림을 방지하는 공정이라 정의할 수 있으며 강제후퇴,석백(Suck Back) 라고도 하며 사출기 스크류가 계량후 회전하지 않고 강제로 후퇴하는 기능입니다
사출 수지의 흐름이 좋지 않은 원재료는 강제후퇴를 사용하지 않아도 상관이 없지만 흐름성이 좋은 원재료는 필히 강제후퇴를 사용하여야 합니다.
노즐홀에서 용융된 수지가 금형으로 흘러내리기 때문에 금형보호도 하고 연속된 작업을 할 수 있기 때문입니다.
(3) 사출압력,사출속도
사출압력은 실린더내의 수지를 금형내로 주입하는 힘을 말하며 사출속도는 노즐에서 금형내로 유입되는 수지의 빠르기를 말합니다.
(4) 사출 냉각시간
사출 성형 제품을 금형으로부터 취출하기 위해서는 금형내에서 일정시간 냉각시켜야 하는데 냉각이 제대로 되지 않은 상태에서 취출하면 제품에 변형이 발생합니다.
사출성형기에는 제품을 냉각 시킬 수 있도록 타이머가 구성되어 있으며 이를 냉각타이머라고 합니다.냉각 타임에 있어 가장 우선적으로 고려해야할 사항은 성형품의 두게이며 성형품 두게에 따라 후변형이 일어나거나 성형품의 치수에 변화가 민감하게 발생할 수있습니다.
냉각라인을 설치 하였으나 밸브를 열지 않고 사출을 진행하는 경우가 발생하기도 하는데 이러한 문제로 금형 온도가 상승하여 제품변형이나 수축 불량이 발생하는 경우도 있으니 주의 하여야 합니다
(5) 사출성형조건 배압,계량속도
플라스틱 사출성형 조건에 있어 배압이란 쉬운 말로 뒤에서 밀어주는 압력이며 사출 계량 공정중 가열실린더내의 스크류가 회전하면서 뒤로 빠질 때 후퇴하는 스크류의 뒤쪽에서 스크류가 빨리 후퇴하지 못하도록 압력을 가하여 밀어준다는 것을 의미하며 배압을 높인다는 것은 스크류가 천천히 밀린다는 의미입니다
사출 성형 조건에 있어 배압을 사용하는 주요 이유는 공기의 혼입방지,휘발분 배출효과,수지의 밀도를 높임,건조스지나 마스터배치의 믹싱을 향상하기 위한 목적입니다.
3. 사출성형 불량현상 및 대책
어떠한 용도의 제품을 생산하느냐에 따라 기업마다 차이점은 있지만 일반적인 사출성형에 있어 불량현상은 다음과 같습니다.
미성형 – 성형품의 일부가 부족하게 만들어지는 현상
성형품의 일부가 부족하게 만들어지는 현상 플래시 – 성형품에 여분의 수지가 붙는 현상
– 성형품에 여분의 수지가 붙는 현상 싱크마크 – 성형품의 표면에 발생하는 오목한 현상
– 성형품의 표면에 발생하는 오목한 현상 웰드라인 – 용융수지가 금형내에서 흐르며 합류한 부분에 생기는 선
– 용융수지가 금형내에서 흐르며 합류한 부분에 생기는 선 플로우마크 – 성형재료의 유동궤적을 나타내는 줄무늬가 생기는 현상
– 성형재료의 유동궤적을 나타내는 줄무늬가 생기는 현상 흑줄 – 성형품의 표면 및 내부에 검은 줄 모양으로 나타나는 현상
– 성형품의 표면 및 내부에 검은 줄 모양으로 나타나는 현상 젯팅 – 게이트에서 캐비티에 분사된 수지가 끈 모양의 형태로 고화하여 성형품 표면이 구불구불한 형태로 나타나는 현상
– 게이트에서 캐비티에 분사된 수지가 끈 모양의 형태로 고화하여 성형품 표면이 구불구불한 형태로 나타나는 현상 이형불량 – 금형에서 성형품이 분리되기 어려운 현상
– 금형에서 성형품이 분리되기 어려운 현상 표층박리 – 성형품이 얇은 층으로 벗겨지는 현상
사출성형불량 미성형,플래시
(1) 미성형 ( Short Shot )
미성형 현상은 사출 수지가 금형 캐비티에 완전히 충진되지 않고 냉각 고화하는 현상이며 미성형의 원인은 수지의 유동성이 부족할 때,사출 압력이 낮을 때 등의 경우 발생하며 이에 대한 대책으로 금형,실린더 온도를 높여 사출 수지가 원할하게 금형내로 유입될 수 있도록 하고 사출 압력을 높여줍니다.
(2) 플래시 ( Flash, Burr )
사출성형 불량 플래시 현상은 금형의 파팅면 등의 틈새에 수지가 흘러들어 정상 성형품 보다 면적이 널어지는 현상으로 사출성형 플래시 불량 원인은 금형내 파팅면의 틈새에 수지가 흘러들러 생기는 현상이며 과도한 사출압력과 속도에 의한 경우가 많으며 사출성형기 형체력 불량일 수도 잇으니 점검이 필요합니다.
사출성형 플랫 불량 방지의 대책으로 금형의 파팅면 보수를 하여야 하고 사출압력,사출속도 등의 사출조건을 조정하여 슴형,실린더등의 온도를 낮추어 수지의 유동성을 조절합니다.
반응형
4. 사출금형 게이트 구조
사출 성형품의 품질은 물론이고 생산 효율 측면,원료의 절감 측면 다양한 측면에서 사출금형의 게이트 구조도 매우 중요하며 사출금형 게이트(GATE) 방식을 살펴보면 다음과 같습니다.
밸브게이트 – 히터를 사용하여 런너 발생없이 제품만 성형시키는 방식,핫트런너 등
– 히터를 사용하여 런너 발생없이 제품만 성형시키는 방식,핫트런너 등 사이드게이트 – 제품 및 런너가 같이 붙어 나오는 형식으로 2단 금형에 사용하며 제품의 후가공이 필요합니다
– 제품 및 런너가 같이 붙어 나오는 형식으로 2단 금형에 사용하며 제품의 후가공이 필요합니다 터널게이트 – 제품 및 런너가 분리되어 취출되는 방식
– 제품 및 런너가 분리되어 취출되는 방식 핀포인트 – 제품과 런너가 금형에서부터 분리되어 취출되는 방식으로 3단금형에서 주로 사용합니다
– 제품과 런너가 금형에서부터 분리되어 취출되는 방식으로 3단금형에서 주로 사용합니다 다이렉트게이트 – 제푸면에 스프루가 붙어 취출되는 ㅂ방식으로 후가공이 필요합니다.
스프루,런너,기이트 구조
스푸루 – 성형재료의 유입부로 원뿔형태를 띠고 사출 성형기의 노즐에서 재료를 받는 주입구 통로
런너 – 성형기 노즐에서 금형 캐비티로 수지가 흘러가는 통로
게이트 – 사출 금형내에서 용융한 성형재료를 캐비티에 주입하기 위한 입구
게이트랜드 – 금형 내부에 있는 캐비티와 런너 사이에 있는 캐비티 길이
콜드슬러그웰 – 열가소성 수지의 사출에 있어 콜드슬러그를 수용하기 위해서 스푸루나 런너의 끝에 수지가 모이는 곳 또는 웰드라인의 강도를 높이기 위해 그 바깥쪽에 설치한 수지가 모이는 곳을 말합니다.
사출성형조건에 미치는 요소
플라스틱 사출 성형조건은 사출성형기,금형,사출재료 등은 물론이고 주변기기와 환경 등 수많은 변수들이 작용하는 종합예술이라 생각합니다.
주조건,보조조건 등이 완벽하여도 결국 운용하는 오퍼레이터에 따른 조건의 변화도 많을 수 밖에 없으며 양질의 제품과 생산성 향상을 위해 표준조건 설정 방법을 연구하여 사전에 성형 불량을 줄이는 노력을 지속적으로 하여야 할 것입니다.
반응형
Top 10 사출 불량 종류 The 112 Correct Answer
#시험사출 #불량종류 #불량별 사출대처법 #사출 노하우 불량 유형별 대처 방법!!!
#시험사출 #불량종류 #불량별 사출대처법 #사출 노하우 불량 유형별 대처 방법!!!
사출성형에 있어서 성형불량의 원인과 대책 : 네이버 블로그
Article author: m.blog.naver.com
Reviews from users: 37229 Ratings
Ratings Top rated: 4.9
Lowest rated: 1
Summary of article content: Articles about 사출성형에 있어서 성형불량의 원인과 대책 : 네이버 블로그 Updating …
Most searched keywords: Whether you are looking for 사출성형에 있어서 성형불량의 원인과 대책 : 네이버 블로그 Updating
Table of Contents:
카테고리 이동
Eco-Nonscale(에코논스케일)
이 블로그
기타자료
카테고리 글
카테고리
이 블로그
기타자료
카테고리 글
사출성형에 있어서 성형불량의 원인과 대책 : 네이버 블로그
Read More
금형사출 불량 사례 모음 – 크렐로
Article author: creallo.com
Reviews from users: 28466 Ratings
Ratings Top rated: 4.8
Lowest rated: 1
Summary of article content: Articles about 금형사출 불량 사례 모음 – 크렐로 금형사출 불량 사례 모음 · 미성형(Short shot) · 플레쉬(Flash/Burr) · 싱크마크(Sink Mark) · 플로우마크(Flow Mark) · 실버 스트릭(Silver Streak) · Cloudy Surface (Gas자국). …
Most searched keywords: Whether you are looking for 금형사출 불량 사례 모음 – 크렐로 금형사출 불량 사례 모음 · 미성형(Short shot) · 플레쉬(Flash/Burr) · 싱크마크(Sink Mark) · 플로우마크(Flow Mark) · 실버 스트릭(Silver Streak) · Cloudy Surface (Gas자국). 3D printing, CNC, Vacuum casting, Injection molding, Quotation, China, Manufacturing, Rapid prototyping, Mockuping금형사출을 이용하여 새로운 부품을 제작하고 대량생산을 할 때, 사출조건, 온도, 소재 등 다양한 변수로 인해 예상했던 품질이 나오지 않을 수 있습니다. 이러한 상황을 예시와 이유 그리고 해결하기 위한 조치사항에 대해서 정리해 보았습니다.금형사출을 이용하여 새로운 부품을 제작하고 대량생산을 할 때, 사출조건, 온도, 소재 등 다양한 변수로 인해 예상했던 품질이 나오지 않을 수 있습니다. 이러한 상황을 예시와 이유 그리고 해결하기 위한 조치사항에 대해서 정리해 보았습니다.
Table of Contents:
금형사출 불량 사례 모음 – 크렐로
Read More
사출 성형 불량 유형 및 해결책 : 네이버 블로그
Article author: m.blog.naver.com
Reviews from users: 22835 Ratings
Ratings Top rated: 3.0
Lowest rated: 1
Summary of article content: Articles about 사출 성형 불량 유형 및 해결책 : 네이버 블로그 사출 성형 불량 유형 및 해결책 · 1. 미성형 (Short Shot) · 2. 버 (Burr, Flash) · 3. 웰드라인 (Weld Line) · 4. 몰드마크 (Mold Mark) · 5. 싱크마크 (Sink … …
Most searched keywords: Whether you are looking for 사출 성형 불량 유형 및 해결책 : 네이버 블로그 사출 성형 불량 유형 및 해결책 · 1. 미성형 (Short Shot) · 2. 버 (Burr, Flash) · 3. 웰드라인 (Weld Line) · 4. 몰드마크 (Mold Mark) · 5. 싱크마크 (Sink …
Table of Contents:
카테고리 이동
(주)플러스허브
이 블로그
공통 성형기술
카테고리 글
카테고리
이 블로그
공통 성형기술
카테고리 글
사출 성형 불량 유형 및 해결책 : 네이버 블로그
Read More
사출성형(플라스틱가공)의 불량 원인과 대책
Article author: dotrazi.tistory.com
Reviews from users: 12329 Ratings
Ratings Top rated: 3.8
Lowest rated: 1
Summary of article content: Articles about 사출성형(플라스틱가공)의 불량 원인과 대책 사출성형(플라스틱가공)의 불량 원인과 대책 · 1. 수분 및 휘발분. ▻ 충분한 건조를 한다. · 2. 수지의 분해 · 3. 공기의 흡입. · 4. 게이트가 작고 사출속도 … …
Most searched keywords: Whether you are looking for 사출성형(플라스틱가공)의 불량 원인과 대책 사출성형(플라스틱가공)의 불량 원인과 대책 · 1. 수분 및 휘발분. ▻ 충분한 건조를 한다. · 2. 수지의 분해 · 3. 공기의 흡입. · 4. 게이트가 작고 사출속도 … 사출성형품의 불량원인과 대책 1. 성형제품의 불량 2. 성형제품설계 불량. 3. 금형설계 불량. 4. 금형가공 제작 불량. 5. 성형기계 불량. 6. 성형기계운전 조건 불량. 7. 원료수지 선택 불량. 8. 원료수지..
Table of Contents:
태그
‘제품개발’ Related Articles
사출성형(플라스틱가공)의 불량 원인과 대책
Read More
품질 관리자가 알려주는 사출 성형 불량 원인
Article author: fean.tistory.com
Reviews from users: 33264 Ratings
Ratings Top rated: 3.6
Lowest rated: 1
Summary of article content: Articles about 품질 관리자가 알려주는 사출 성형 불량 원인 사출 성형 불량 원인 · 쇼트 (Short Shot) · 금형 상처, 긁힌 상처 (Mold Mark) · 플래시 (Flash) 또는 버 (Burr) · 싱크 마크 (Sink Mark) · 웰드 라인 (Weld … …
Most searched keywords: Whether you are looking for 품질 관리자가 알려주는 사출 성형 불량 원인 사출 성형 불량 원인 · 쇼트 (Short Shot) · 금형 상처, 긁힌 상처 (Mold Mark) · 플래시 (Flash) 또는 버 (Burr) · 싱크 마크 (Sink Mark) · 웰드 라인 (Weld … 품질 관리 업무를 사출이나 프레스 관련 업체에서 하고 있다면, 사출 성형 불량 원인을 꼭 숙지해야 한다. 그래야 업무를 능숙하게 이끌어 갈 수 있다. 품질 관리 업무를 하면서 제대로 된 성형 불량 원인도 모르..
Table of Contents:
사출 성형 불량 원인
Comments
품질 관리자가 알려주는 사출 성형 불량 원인
Read More
사상 사출금형과 사출불량의 종류 – 사출금형의 정보 – 1조모임
Article author: m.cafe.daum.net
Reviews from users: 8052 Ratings
Ratings Top rated: 3.4
Lowest rated: 1
Summary of article content: Articles about 사상 사출금형과 사출불량의 종류 – 사출금형의 정보 – 1조모임 사상 사출금형과 사출불량의 종류 · 1) 미성형(Short Fill) · 2) 표면수축(Sink) · 3)버어(Burr) · 4) 웰드 라인(Weld Line) · 5) 은조(Silver Streak) · 6) … …
Most searched keywords: Whether you are looking for 사상 사출금형과 사출불량의 종류 – 사출금형의 정보 – 1조모임 사상 사출금형과 사출불량의 종류 · 1) 미성형(Short Fill) · 2) 표면수축(Sink) · 3)버어(Burr) · 4) 웰드 라인(Weld Line) · 5) 은조(Silver Streak) · 6) … 모든 이야기의 시작, Daum 카페
Table of Contents:
사출금형의 정보
카페 검색
사상 사출금형과 사출불량의 종류 – 사출금형의 정보 – 1조모임
Read More
사출 불량 유형 – 수축(Sink Mark) | TechBox
Article author: techgoogleblogger.blogspot.com
Reviews from users: 3722 Ratings
Ratings Top rated: 4.7
Lowest rated: 1
Summary of article content: Articles about
사출 불량 유형 – 수축(Sink Mark) | TechBox
사출금형불량유형 – 수축(Sink Mark). 제품의 표면에 움푹 패여 보이는 부분을 수축(sink mark)이라고 한다. 싱크마크는 성형불량 현상 중 가장 발생 … …
사출 불량 유형 – 수축(Sink Mark) | TechBox 사출금형불량유형 – 수축(Sink Mark). 제품의 표면에 움푹 패여 보이는 부분을 수축(sink mark)이라고 한다. 싱크마크는 성형불량 현상 중 가장 발생 … … Most searched keywords: Whether you are looking for
사출 불량 유형 – 수축(Sink Mark) | TechBox
사출금형불량유형 – 수축(Sink Mark). 제품의 표면에 움푹 패여 보이는 부분을 수축(sink mark)이라고 한다. 싱크마크는 성형불량 현상 중 가장 발생 … 사출 불량 유형 – 수축(Sink Mark)
사출 불량 유형 – 수축(Sink Mark) | TechBox 사출금형불량유형 – 수축(Sink Mark). 제품의 표면에 움푹 패여 보이는 부분을 수축(sink mark)이라고 한다. 싱크마크는 성형불량 현상 중 가장 발생 … 사출 불량 유형 – 수축(Sink Mark) Table of Contents:
Search
인기글
최근글
Tag
댓글
페이지
블로그 보관함
프로필
라벨
링크
사출 불량 유형 – 수축(Sink Mark) | TechBox
Read More
[ÇÃ¶ó½ºÆ½»ê¾÷Æ÷ÅÐ – ÇÃ¶ó½ºÆ½³Ý ÀÔ´Ï´Ù] ¼ºÇüºÒ·®Çö»ó°ú ´ëÃ¥Article author: www.plasticnet.kr
Reviews from users: 30541 Ratings
Ratings Top rated: 3.5
Lowest rated: 1
Summary of article content: Articles about [ÇÃ¶ó½ºÆ½»ê¾÷Æ÷ÅÐ – ÇÃ¶ó½ºÆ½³Ý ÀÔ´Ï´Ù] ¼ºÇüºÒ·®Çö»ó°ú ´ëÃ¥ 이하에 사출성형의 중요한 불량현상과 그 직접적인 원인에 대해서 설명해 그들 … 사출능력(용량, 가소화능력) 부족 … 또한 어떤 종류의 화학성분에 접촉시키면 …
Most searched keywords: Whether you are looking for [ÇÃ¶ó½ºÆ½»ê¾÷Æ÷ÅÐ – ÇÃ¶ó½ºÆ½³Ý ÀÔ´Ï´Ù] ¼ºÇüºÒ·®Çö»ó°ú ´ëÃ¥ 이하에 사출성형의 중요한 불량현상과 그 직접적인 원인에 대해서 설명해 그들 … 사출능력(용량, 가소화능력) 부족 … 또한 어떤 종류의 화학성분에 접촉시키면
Table of Contents:
[ÇÃ¶ó½ºÆ½»ê¾÷Æ÷ÅÐ – ÇÃ¶ó½ºÆ½³Ý ÀÔ´Ï´Ù] ¼ºÇüºÒ·®Çö»ó°ú ´ëÃ¥Read More
플라스틱 사출성형 조건 불량원인 및 대책 – 산비탈 사는 이야기
Article author: sanvital.tistory.com
Reviews from users: 40098 Ratings
Ratings Top rated: 3.6
Lowest rated: 1
Summary of article content: Articles about 플라스틱 사출성형 조건 불량원인 및 대책 – 산비탈 사는 이야기 1. 사출성형 설비의 종류 및 성형 공정. 수평 사출성형기. 사출성형 설비의 종류는 수평식 사출기에 직압식 … …
Most searched keywords: Whether you are looking for 플라스틱 사출성형 조건 불량원인 및 대책 – 산비탈 사는 이야기 1. 사출성형 설비의 종류 및 성형 공정. 수평 사출성형기. 사출성형 설비의 종류는 수평식 사출기에 직압식 … 플라스틱 사출성형 조건 사출 불량원인 및 대책 사출 성형이란 플라스틱(RESIN)에 열을 가하여 가소화 시킨후 유압으로 용융수지를 금형에 주입하여 원하는 형상의 제품을 만들어 내는 것을 말합니다. 사출성형에..
Table of Contents:
플라스틱 사출성형 조건 불량원인 및 대책 – 산비탈 사는 이야기
Read More
See more articles in the same category here: https://toplist.xosotanphat.com/blog.
사출성형에 있어서 성형불량의 원인과 대책
사출성형에 있어서 성형불량의 원인과 대책 사출 성형에 있어서 성형 불량의 원인은 크게 10가지 정도로 구분될 수 있습니다. 1. 충전 부족 (Short Shot) 2. 흑줄 (Black streak) 3. 크랙 (Crack) 4. 플래시 (Flash, Burr) 5. 플로우 마크 (Flow Mark) 6. 젯팅 (Jetting) 7. 싱크 마크 (Sink Mark) 8. 은줄 (Silver Streak) 9. 휨 / 변형 (Warpage) 10. 웰드 라인 (Weld Line) 다음 10가지의 불량의 원인과 대책에 대하여 포스팅 해보려 합니다. 1. 중전 부족 (Short Shot) 수지가 캐비티에 완전히 충전되지 않고 냉각 고화하는 현상 대책 1) 다수개폐기의 경우 일부가 충전 불량일때 : 게이트 밸런스 불량이므로 게이트 밸런스 보정 2) 수지의 유동성 부족 : 사출온도를 높이거나 사출압력 또는 속도를 높임, 유동성이 높은 수지 선정 3) 사출기 용량에 비해 금형이 큰경우 : 사출기 용량이 큰것으로 교체 4) 금형내 유동저항이 큰경우 : 유동저항을 크게 받는 부분의 직경을 증가시킴 5) 캐비티 내 공기가 빠지지 않음으로써 생기는 경우 : 사출속도를 낮춤으로써 공기가 빠져나갈 시간을 준다. 6) 호퍼에서의 수지 공급 부족 A) 호퍼부의 과열로 호퍼에 Pellet이 붙어 낙하하지 않음 : 호퍼부 온도를 낮추거나 냉각수를 사용, 호퍼부 온도를 떨어뜨린다. B) 윤활성이 과다한 Pellet으로 스크류가 Pellet을 앞으로 보내지 못함 : 윤활성이 적은 Pellet 사용 2. 흑줄 (Black streak) 성형물에 흑갈색의 흐름 모양이 나타나는 현상 대책 1) 금형 표면에 기름등이 부탁되어 있는 경우 : 금형 표면에 기름, 그리이스가 묻어있거나 이젝터 편에서 기름, 그리이스 등이 나오는 경우로 금형 표면을 깨끗한 상태로 유지하도록 한다. 2) Hot-Runner의 색상 교체 불량인 경우 ( Manifold 내에 체류 된 수지가 남아 있어 Gate 부근에 흑줄 발생) : 기존 수지가 체류되지 않도록 MainFold의 구조변경 3) 수지의 열분해에 의한 경우 : 실린더 내의 체류시간을 적게 하거나 과열을 방지 수지온도를 내리고 사출속도를 느리게 한다. 때때로 퍼징을 하는 것도 좋다. 4) 호퍼 부근의 냉각의 불충분한 경우 (수지가 공급될 때 공기가 같이 들어가면 이 공기에 의해 수지가 타게 되어 발생) : 호퍼부의 냉각수 양을 늘리고, 호퍼다음의 실린더 온도를 낮춘다. 5) 사출기 손상에 의한 경우 (실린더 배부나 역류방지 밸브 등이 타서 부서진 경우 발생) : 이 경우 노즐의 조임 부분 등에서 탄 수지가 많이 나오므로 신속한 교체 필요 3. 크랙 (Crack) 성형물 표면에 금이 가는 현상 대책 1) 잔류응력에 의한 경우 : 캐비티 과충전에 의한 경우, 불균일한 살 두께에 의한 경우, 이형 시에 발생하는 경우 인서트 주위에 발생하는 경우, 금형온도 또는 수지 온도가 부적당한 경우 2) 외부 응력에 의한 경우 : 성형품 형상 불량에 의한 응력의 집중, 후 가공 시 외부응력에 의한 경우, 반복 / 진동 하중에 의한 경우, 열팽창 수축에 의한 경우 3) 환경 응력에 의한 경우 : 화학약품에 의한 경우, 열에 의한 경우, 자외선에 의한 경우 4) 금형의 빼기 구배 부족인 경우, 금형면의 연마불량 5)캐비티 과충전에 의한 경우 (가장 많은 압력이 걸리는 게이트 부근에 크랙 발생) : 수지의 유동성을 높여 낮은 사출압력으로 성형, 실린더 온도를 높이거나 사출속도를 빠르게 한다. 6) 금형 온도가 부적절한 경우 : 금형 온도가 불균일한 경우 냉각차에 의한 응력이 발생한다. 7) 불균일한 제품 두께에 의한 경우 (두꺼운 부분의 냉각이 불충분한 상태에서 취출 시 이젝터 핀 주위에 발생) : 충분한 냉각시간을 주거나 성형품의 두께가 면하는 부위에 R 또는 테이퍼 처리를 한다. 8) 사출조건에 의해 해결이 불가능한 경우 강도, 분자량이 높은 수지로 재료 변경 필요. 4. 플래시 (Flash, Burr) 금형의 파팅면 등의 틈에 수지가 흘러 정상 성형물보다 면적이 넓어지거나 중량이 늘어나는 것 대책 1) 금형 파팅면 불량에 의한 경우 : 금형 파팅 면의 보수 필요 2) 과도한 사출 압력과 사출속도 (냉각 시 압력이 가장 높은 게이트 부나 런너 부근에 발생) : 사출 압력과 사출 속도를 낮춘다. 3) 형체압이 부족한 경우 (성형품 투영 면적에 비해 형체력이 작은 경우) : 높은 형체력을 갖는 사출기로 교체 필요 4) 성형기의 보수 관리가 나쁜 경우 (유지 관리가 불량하면 형체력에 좌우, 상하 불균형이 생겨 발생) : 주기적으로 성형기 점검이 필요 5. 플로우 마크 (Flow Mark) 대책 1) 게이트 부가 필요이상으로 냉각되는 경우 (수지 온도 저하가 현저해 지고 고점도가 된다.) : 금형 파팅면의 보수 필요 2) 수지 점도가 높은 경우 (수지 점도가 너무 높으면 충분한 사출압력을 전달 할 수 없다.) : 수지 온도와 금형 온도를 높이고 사출 속도를 빠르게 함으로써 수지 점도의 증가를 막는다. 3) 금형 온도가 낮은 경우 (수지, 냉각이 빠르게 일어나 수지 점도가 급격히 증가한다.) : 금형 온도 제어기를 이용하여 적절한 온도로 금형 온도를 유지한다. 4) 사출 속도가 느린경우 (캐비티 충진 속도가 늦어진다.) : 금형온도, 수지온도를 높여서 늦은 사출 속도로 인하여 충진 도종 수지가 빼앗기는 열량을 보충한다. 6. 젯팅 (Jetting) 성형물 표면에 케이트로 부터 리본 모양의 흐름자국 대책 1) 게이트 구조불량 (게이트가 작거나 얇은 부분에서 사출된 수지의 유속이 갑자기 빨라져 발생) : 게이트의 단면적을 넓힌다. 게이트 단면적 X 유속 = 사출량 게이트의 가로와 세로비는 1:3~1:2가 적당하다 2) 콜드 슬러그 웰이 작거나 없는 경우 (노즐 통과 시 냉각된 수지가 런너에서 다시 냉각되어 캐비티에 사출되어 그대로 냉각되며 발생) : 콜드 슬러그 웰을 만들거나 너무 작은 경우 크기를 크게한다. 3) 금형 온도가 낮은 경우 (금형 내에서 수지가 급냉되어 발생) : 금형온도는 사용 수지의 열변형 온도보다 20℃ 정도 낮은 온도가 적당하다. 4) 수지점도가 높은 경우 (수지 점도에 비해 사출온도가 낮은 경우) : 노즐 부분의 온도를 높인다. 7. 싱크 마크 (Sink Mark) 제품의 두꺼운 부분이나 리브(Rib), 보스(Boss) 등의 외츠면이 불충분한 냉각에 의해 안쪽으로 빨려 들어오는 현상 대책 1) 스프루, 런너, 게이트가 작은경우 (냉각 고화가 빨리 일어나 압력강하가 커지고 캐비티 내에 압력을 충분히 전달 할 수 없다.) : 압력 전달이 충분히 될 수 있도록 케이트, 런너의 크기를 크게 한다. 2) 금형 온도가 부적절한 경우 (성형품의 두께가 두꺼운 부분이나 리브 부분은 다른 부분에 비해 냉각이 늦으므로 안으로 함몰됨) : 리브 부분이 충분히 냉각될 수 있도록 구조를 조절한다. 3) 사출조건상의 원인 A) 사출압이 낮은 경우 : 사출압을 증가시킨다. B) 사출압 유지 시간이 짧은 경우 : 수지의 열 수축이나 역류가 일어나지 않도록 보압 유지 시간을 길게 한다. C) 쿠션량이 부적절한 경우 : 쿠션량이 너무 적으면 압력이 전달되지 않으며, 너무 많은 경우에는 압력이 실린더 전부에 있는 수지에 흡수되어 버리므로 적절한 양을 유지한다. (3 ~ 5 mm) 8. 은줄 (Silver Streak) 재료의 유동방향으로 은백색의 줄이 생기는 현상 대책 1) 게이트 구조불량 (게이트가 작거나 얇은 부분에서 사출된 수지의 유속이 갑자기 빨라지고 압력이 높아져 수지가 분해를 일으키며 발생) : 엔지니어링 플라스틱의 주요 발생원인 게이트의 단면적을 넓힌다. 2) 금형 표면 불량 (표면의 수분, 유분, 이형제 등이 용융수지 열에 의해 증발하여 가스가 되어 성형품에 발생) : 금형 표면을 알코올, 용제 등으로 청소 3) 사출압이 높거나 속도가 빠른 경우 (급격한 살 두께의 변화가 있을 때 유동 중 압축된 수지가 급격히 감압되어 팽창하면서 휘발분이 가스화 되었다가 금형면과 접촉 시 액화 되면서 발생) : 사출압을 낮추고 속도를 느리게 하여 휘발 가스가 충분히 배기 되도록 한다 4) 수지온도, 금형온도가 너무 낮은 경우 (수지의 냉각 고화가 빨라서 배기가 불충분하기 때문에 발생 : 수지와 금형 온도를 높여 냉각 고화를 느리게 한다 5) 수지의 열분해에 의한 경우 (수지 자체 또는 안정제,안료 등 첨가제가 분해되어 발생) : 불균일한 가소화나 체류에 의해 발생하므로 성형기 최대사출용량의 30 ~ 60% 범위에서 조작되도록 한다 6) 스크류 내에 공기가 혼입된 경우 : 배압이 없는 경우 혼입되기 쉽다 호퍼 하부의 냉각을 충분히 하고 실린더 후부 온도와 스크류 회전 수를 내린다 SUCK BACK 양을 줄인다 7) 수지의 수분 및 휘발분에 의한 경우 : 성형 전 충분한 건조로 수분이나 휘발분 제거 장마 때와 같이 공기 중에 수분이 높은 경우 호퍼에 수분이 맺혀 발생하기 쉽다 8) 재생 수지 사용에 의한 경우 (불균일한 형태의 재료가 혼입될 때 재료 사이의 공극으로 공기가 혼입) : 재생 수지를 사용할 경우 입자 크기를 균일하게 한다 9. 휨 / 변형 (Warpage) 대책 1) 냉각이 불균일한 경우 (성형품 부분간 냉각속도가 다를 때 발생 빨리 냉각되는 곳은 수축이 작고 늦게 냉각되는 곳은 수축이 크므로 발생) : 같은 속도로 냉각이 되도록 냉각라인 설치 게이트에서 멀 수록 수지온도가 낮아지므로 냉각 라인은 게이트 부근에서 먼 곳으로 향하게 한다 2) 부적절한 게이트 (게이트 위치가 부적절하여 캐비티 내의 충전시간에 차이가 큰 경우) : 게이트 위치 변경 먼저 충전된 부분과 나중에 충전된 부분의 수축율이 틀려서 발생 10. 웰드 라인 (Weld Line) 캐비티내에서 2개 이상의 분류된 흐름이 다시 합류할 때완전히 융합되지 않고 실모양의 가는 선으로 나타나는 현상 대책
사출성형(플라스틱가공)의 불량 원인과 대책
사출성형품의 불량원인과 대책 1. 성형제품의 불량 2. 성형제품설계 불량. 3. 금형설계 불량. 4. 금형가공 제작 불량. 5. 성형기계 불량. 6. 성형기계운전 조건 불량. 7. 원료수지 선택 불량. 8. 원료수지 처리, 첨가제 등의 불량. Burr 불량 금형고정측과 가동측사이,슬라이드부분,insert의 틈새, 밀핀의 간격등에 수지가 들어가 제품에 필요이상의 지느러미가 생기는 현상. 주원인과 대책: ① 금형의 맞춤면, 분할면 등의 불량. ► 4개 또는 2개의 타이바를 균등하게 조정. ► 슬라이드 코아의 밀어젖힘력을 충분하게 한다. ► 좌우 분할금형은 사출압력에 견딜 수 있는 투영면적을 준다. ② 형체력 부족에 의함. ► 사출압력을 낮추거나 형체력을 높인다. ③ 수지의 점도가 낮음. ► 사출속도를 낮추거나, 금형의 온도를 낮춰서 점도를 저하시킨다. ► 캐비티 용적에 비해 수지 공급량이 과다 하지 않도록 주의한다. ④ 금형 사이에 이물이 끼어 있음. 수축불량(sink mark) 성형품 표면에 움푹 파인 현상. 주 원인과 대책 : ① 사출압력이나 보압이 부족하여 발생되는 수축. ► burr가 발생되지 않는 범위 내에서 사출압력을 높여주고 보압 시간을 길게 한다. ② 충분한 사출압력에도 발생되는 수축. ► 스프루나 런너,게이트의 직경이 작은지 검토한다. ③ 금형냉각량이 부족하거나 금형온도 불 균일. ► 냉각수 온도나 구조상 문제가 있는지 확인한다. ► 수축이 심한 boss나 rib부위는 냉동기를 활용하여 차가운 냉각수가 흐르게 한다. ④ 성형품의 살 두께 불 균일. ► 설계시 살 두께가 균일하게 해주고 불균일한 곳은 살 빼기, 살 붙이기를 해준다. ⑤ 살 두께가 너무 얇거나 게이트에서 멀 경우 발생. ► 게이트에서 멀면 수지가 흐르는 도중에 식어버려 수축이 발생된다. 스프루,런너, 게이트를 크게 하고 금형온도를 높인다. 은줄(Silver streak) 수지흐름 방향으로 은색, 백색의 자국이 흩어지듯 생기는 현상. 주 원인과 대책 : 1. 수분 및 휘발분 ► 충분한 건조를 한다. 2. 수지의 분해 ► 정전기 방지제나 난연제, 방청제등의 첨가제로 인해 생기기 쉽다. ► 수지가 분해하지 않도록 수지온도를 내리고, 실린도내에 체류시간을 짧게 한다. 3. 공기의 흡입. ► 수지가 들어갈 때 공기가 함께 들어가 생김. 4. 게이트가 작고 사출속도가 빠르면 발생. ► 사출 속도를 줄이고 게이트를 크게 한다. 5. 스크류 마찰열에 의한 발생 ► 스크류 회전수가 너무 빠르지 않게 주의 6. 수지온도 저하 ► 수지온도가 너무 높으면 가스를 빼 내지 못함. 7. 가스가 빠지지 않아서. ► 에어밴트를 설치해준다. 8. 금형온도가 낮을 때. ► 수지의 흐름이 차단되면 은줄이 생긴다. 미성형(Short shot) 설계로 목적했던 제품의 형상이 나오지 않는 현상. 주 원인과 대책 : 1. 성형기계의 능력 부족. ► 공급능력이 부족한 기계의 경우 발생. 2. 성형재료. ► 첨가제를 넣은 재료는 유동성이 나빠 나올 수 있다. (가열실린더 온도를 높이고 압력을 높여 작업한다.) 3. 수지온도가 일정기준보다 낮을 때. ► 가열실린더 온도를 높이고 압력을 높인다. ► 금형의 온도를 높인다. 4. 리브나 보스에 발생. ► 가능한 분할 코어를 이용하여 가스를 제거해줌. 5. 금형 파팅 라인이 가스벤트 역할을 못함. ► 파팅면의 이물을 수시로 제거해줌. 6. 캐비티가 두 개 이상인데 일부가 미성형. ► 게이트밸런스와 성형품의 살 두께가 맞지 않음. 웰드라인(Weld line) 수지가 합류하는 부분에 가느다란 실선이 생기는 현상. 주 원인과 대책 : 1. 게이트가 여러 개소에 있다. ► 게이트 수를 줄이거나 위치를 옮기고, 사출압력과 속도를 조절한다. 2. 게이트와 상관없는 부분에 생김 ► 살 두께에 편차가 있는 경우에 생기며 얇은 부분은 살 붙이기를 해 준다. 3. 공기 또는 휘발분의 유입. ► 에어밴트를 설치해준다. 4. 수지온도가 낮을 경우. ► 수지온도를 높여주어 수지가 합류할 때 융합하게 한다. 5. 금형온도가 낮을 때 ► 온도를 높여 수지가 잘 융합하게 한다. 6. 사출압력, 보압 시간이 적을 때. ► 압력을 높이고 보압 시간을 길게 하면 앞단부에서 고화되는 것을 막을 수 있다. 7. 건조가 충분치 않은 경우 발생 할 수 있으므로 충분히 건조한다. 8. 설비 개선을 통한 대책 1) 유도전열장치 ► 웰드가 발생하는 곳에 유도전열장치를 설치하여 순간적인 온도를 급상승하여 웰드를 없애는 방법. 2) 로직 시일 방식 ► 로직 시일 방식 강제가스 빼기 장치를 활용하는 방법으로 냉각회로를 이용하여 공기를 흡입하는 방식. 3) 급냉, 급열 온도 조절방식. ► 사출시 금형온도를 고온으로 하고 완료시 금형을 순간적으로 급랭하는 방식. 휨(warp),굽힘(Bending),뒤틀림(Twisting) 수지흐름에 따라 휨이나 변형불량이 생김. 주 원인과 대책 : 1. 금형온도가 낮은 쪽으로 휨이 발생. ► 온도를 균일하게 하던지, 낮은쪽을 높여준다. 2. 금형온도가 부분적으로 다르다. ► 금형 냉각회로를 점검한다. 3. 사출압력이 너무 높거나 낮으면 발생. ► 압력이 높으면 열팽창에 의해 생김. ►낮으면 융합이 약해 휨이 발생할 수 있다. 4. 냉각이 충분히 안됨. ► 밀핀의 힘으로 휨이 발생할 수 있으므로 냉각을 충분히 해주던지 밀핀을 고루 분포시킨다. 5. 수지의 유동성이 나쁘다. ► 수지의 흐름방향의 수축률이 직각방향으로 흐르는 수축률보다 클 경우 발생.(리브를 설치하는 등 설계의 일부를 변경한다.) 6. 잔류응력에 의함 휨. ► 어니링을 실시한다. 7. 설계에 의한 휨 발생 ► 살 두께를 균일하게 해준다. ►리브를 설치하여 휨을 방지한다. 치수불량 성형조건의 변화, 계절변화, 밤과 낮의 기온차, 성형재료의 Lot 변화, 설계시의 살 두께 편차, 금형제작시의 정밀도 부족등이 있다. 주 원인과 대책 : 1. 사출압력과 속도가 너무 높거나 낮다. ► 너무 높으면 치수초과나 burr가 발생되며, 너무 낮으면 치수미달이나 미성형, 수축불량이 나온다. 2. 금형온도 ► 금형온도를 일정하게 유지시킨다. 3. 냉각시간이 짧음. ► 응력회복이 커지고 성형품의 밀도가 높아지므로 수축이 생김. 4. 환경에 의한 치수변화 ► 계절, 밤과 낮에 따라 치수가 변할 수 있으므로 공장은 항상 일정한 온도와 습도를 유지하게 한다. 5. 형체력에 의한 불량. ► 형체력이 너무 높을 경우 가스가 빠지지 못해 치수가 작아진다. 흑점 및 흑줄 발생 공기가 압축과 고온으로 인한 열로 수지가 타는 현상. 주 원인과 대책 : 1. 성형재료에 의한 발생 ► 난연제를 첨가한 성형재료는 수지온도를 최소화하여 가열 실린더 온도를 설정한다. ► 수지를 이물이 첨부되지 않도록 주의 보관한다. ► 실린더 내에 잔량을 최소화 한다. 2. 성형조건에 의한 불량 ► 가열실린더 온도를 필요이상 높게 하지 않는다. ► 스크류회전수와 사출속도를 빠르게 하여 마찰열을 상승시키지 않는다. ► 호퍼 밑 부분이 냉각이 제대로 되지 않으면 탄화현상이 생긴다. 3. 사출성형기에 의한 불량 ►실린더와 스크류 사이가 벌어져 수지가 조금씩 나오면서 불량이 발생된다. ► 노즐과 실린더 간에 벌어지면 틈 부위네 체류되어 있던 수지가 탄화되어 불량이 생긴다. ►실린더를 세척한다. 플로우 마크(Flow mark) 게이트 중심으로 반달 혹은 띠를 형성한 모양. 금형 내에 최초로 유입되는 수지의 냉각이 너무 빠르기 때문에 다음에 흘러 들어오는 수지와의 사이에 경계가 생겨 발생한다. 주 원인과 대책 : 1. 성형재료에 의한 플로우 마크 ► 예비 건조를 한다. ► 실린더와 금형온도를 높여 유동을 좋게 한다. 2. 성형조건에 의한 불량. ► 사출속도를 높이거나 낮게 하여 마찰열을 조절한다. ► 사출압력을 높이고 보압 시간을 다소 길게 한다. 3. 설계에 의한 불량 대책 ► 살 두께 변화를 완만히 하여 흐름을 좋게 한다. ► 에어벤트를 설치하여 가스빼기를 한다. ► 게이트부에 콜드 슬러그 엔을 설치한다. 젯팅 불량 사이드게이트와 오버랩게이트에 많이 생기며 수지가 끈 모양의 형태로 고화해서 성형품의 표면에 꾸불꾸불한 모양을 나타내는 현상. 주 원인과 대책 : 1. 유입되는 수지의 유속이 너무 빠르거나 유로가 길면 생기기 쉽다. 2. 차가운 수지가 금형내부를 통과한 후, 나중에 들어오는 뜨거운 수지가 흐를 때 표면으로 자국을 남김. ► 게이트를 재료의 두께방향으로 캐비티의 벽 근거리에 설치한다. ► 수지가 고화 되지 않도록 수지의 온도를 높인다. ► 콜드 슬러그웰을 설치하여 앞단부에 차가운 수지가 들어가지 않도록 한다. ► 게이트를 크게 한다. 크랙, 백화 크랙 : 성형품의 한 부분이 깨지거나 금이 가는 현상. 백화 : 깨지면서 발생되는 흰 부분, 또는 밀핀의 힘에 의해 억지로 빠질 때 자국으로 남는 현상. 주 원인과 대책 : 1. 사출압력에 의한 불량. ► 과 충전되면 내부응력이 발생되어 크랙이 발생되기 쉽다. 2. 잔류응력 ► 사출 압을 너무 높이면 잔류응력이 발생될 수 있다. 3. 이형불량 ► 충분한 빼기 구배를 준다. 4. 냉각 불충분에 의한 불량. ► 고화가 덜 된 상태에서 밀핀 주위가 깨지거나 백화가 발생할 수 있다. 5. Insert 주위가 깨지는 현상. ► 인서트는 수축하지 않고 수지만 수축하는 상태에서 응력이 집중 될 수가 있다. 제품개발,제품설계, 중국금형은 엑스코어에서! http://www.thexcore.com
품질 관리자가 알려주는 사출 성형 불량 원인
반응형 품질 관리 업무를 사출이나 프레스 관련 업체에서 하고 있다면, 사출 성형 불량 원인을 꼭 숙지해야 한다. 그래야 업무를 능숙하게 이끌어 갈 수 있다. 품질 관리 업무를 하면서 제대로 된 성형 불량 원인도 모르고 무조건 NG 처리하여 반품하는 경우도 많다. 기구 설계나 금형 설계 구조에 따라 문제가 발생하는 경우도 있다. 따라서 품질 관리자는 사출 성형 불량의 원인을 알고 그에 따른 합리적인 대책을 제시해야 한다. 이번 포스팅은 품질 관리자가 꼭 알아야 하는 사출 성형 불량 원인을 정리하였다. 사출 성형 불량 원인 쇼트 (Short Shot) 성형할 수지가 충분히 가열되지 않거나, 사출 압력 및 금형 온도가 매우 낮을 경우, 금형 전체에 수지가 들어가지 않고 냉각 고화해서 성형품 일부가 모자란 현상이다. 금형 상처, 긁힌 상처 (Mold Mark) 금형 상처는 금형 표면의 상처가 제품 표면에 나타나는 현상이다. 금형을 수정하면 고칠 수 있다. 긁힌 상처는 금형의 역테이퍼 또는 테이퍼 부족으로 제품과 금형 마찰면에 생기는 상처이다. 수리하지 않으면 계속 상처가 발생한다. 플래시 (Flash) 또는 버 (Burr) 금형의 맞춤면 주로 파팅라인 (Parting Line)에서 자주 생긴다. 즉, 고정형과 이동형의 사이, 슬라이드 부분, insert 틈새, ejector 핀 간격 틈새, gas vent 주위 등에 수지가 흘러들어 가 필요 이상의 지느러미가 생긴 현상이다. 플래시 (Flash) 또는 버 (Burr)는 한번 발생하면 이후에 나오는 제품들은 더 큰 플래시가 생기게 된다. 금형을 오목하게 만들어 플래시가 더 커지므로 처음부터 발생하지 않도록 해야 하며, 플래시가 발생하면 금형을 수정한다. 주로 금형 맞춤면, 분할면 등 불량, 형체력 부족, 수지 용융 점도가 낮음, 금형 사이에 이물 등을 원인으로 꼽을 수 있다. 싱크 마크 (Sink Mark) 싱크 마크는 성형품에 있는 함몰된 부분을 말한다. 가장 많이 일어나는 성형 불량이다. 보통 수지의 성형 수축에 의해 발생하여 제거하기 어려운 부분이 있다. 사출성형은 냉각된 금형 용융 수지를 주입할 때 금형에 접촉한 면부터 냉각되고, 수지는 열전도가 나빠지고 매우 복잡한 현상이 생긴다. 금형에 접하는 표면이 빨리 냉각되어 고화, 수축하고 내부는 냉각이 늦으므로 수축도 늦는다. 빨리 수축하는 쪽으로 재료는 움직이고, 늦게 수축하는 부분은 수지량이 부족해서 기포가 된다. 싱크 마크는 성형품의 냉각이 비교적 늦은 부분으로 표면이 내부의 기포발생을 없애는 방향으로 끌려서 오목면이 되는 현상이다. 즉 성형품의 두꺼운 부분에서 발생하기 쉽다. 수축이 큰 수지에 심하다 : 폴리프로필렌, 폴리에틸렌, 폴리아세탈 등 성형품의 살 두께가 불균일하다. 금형의 냉각이 불균일하거나 불충분하다. 금형 내 압력이 부족해서 충분히 압축되지 않는다. 사출 속도가 너무 빠르다. 재료의 수축이 큰 것 등이다. 웰드 라인 (Weld Line ; Weld Mark) 웰드 라인은 용융 수지가 금형 내를 분기해서 흐르다가 합류한 부분에서 생기는 가는 선을 의미한다. 성형 시 구멍이 있거나 insert가 있을 때 발생한다. 웰드 라인은 2개의 게이트로 성형할 때도 발생하는데 게이트 위치를 변경하여 웰드 라인을 눈에 잘 보이지 않게 위치를 바꾸는 것 이외에 다른 방법은 없다. 웰드 라인은 분기해서 흐른 용융 수지의 앞쪽 부분이 다시 합류할 때까지 냉각되어 완전히 융합하기 어려워 합류하는 곳에 줄이 발생한다. 웰드 부분은 융합이 완전하지 않아 강도 저하가 발생하므로 반드시 고려해야 할 부분이다. 플로우 마크 (Flow Mark) 플로우 마크는 수지가 흐른 자국이 나타나는 것이다. 형태는 게이트 중심으로 동심원의 얼룩무늬, 광택, 표면 거칠어짐이 발생한다. 원인은 금형에 처음 유입한 수지의 냉각이 너무 빠르기 때문에 다음에 흘러 들어오는 수지와의 사이에 경계가 발생한다. 이는 수지의 정도가 지나치게 높고 수지 온도와 금형 온도가 불균일하거나 성형품의 살 두께 변화가 많고 단차가 급한 것에 발생하기 쉽다. 광택불량(표면흐림)과 가스자국 광택 불량과 가스 얼룩은 성형품의 표면이 원래 광택과 다르고 유백색의 막이 덮여 안개 낀 듯한 상태가 되는 현상을 의미한다. 원인은 금형 표면에 수지가 충분히 밀착하지 못하고, 가스가 금형 표면에 응축해서 금형면에 접착을 방해한다. 그 외 금형의 연마 부족, 윤활제, 이형제 과다 도포도 원인이다. – 자료 출처 : 최신 제품 설계 [이국환] – 이미지 출처 : 네이버 사출금형/성형기술 카페, 작성자 미카엘(caild77) 반응형
So you have finished reading the 사출 불량 종류 topic article, if you find this article useful, please share it. Thank you very much. See more: 사출 불량 용어, 사출 침식 불량, 사출 흑줄, 사출 압, 플라스틱 사출 불량, 사출 흑점 불량, 사출 수축 원인, 사출 젯팅
사출성형 불량의 유형 및 대책-4 (웰드라인, 보이드, 싱크마크, 숏샷, 버)
웰드 라인
발생원인
웰드 라인이랑 캐비티 내에 무엇인가의 장애물이 있어 수지가 분단되어 다시 합류하거나, 다점 게이트를 사용했을 때에 수지가 합류하는 부분에 발생하는 융합 불량 현상이다. 성형품에 선상의 모양을 남겨 외관적으로도 나쁠 뿐만 아니라 강도상으로도 취약해진다. 또 이외에 성형품의 살 두께 변동에 의한 웰드 라인도 있다.
캐비티 내의 장애물에 의한 웰드라인 대책
금형 온도를 높게한다
수지 온도를 높게한다
사축 속도를 빠르게 한다
사출 압력을 높게 한다
금형에 탭을 설치한다
살 두께의 변화에 의한 웰드라인 대책
금형 온도를 높게한다
수지 온도를 높게한다
사축 속도를 느리게 한다
보이드(공동)
발생원인
살이 두꺼운 성형품에 많이 발생하는 불량으로 살이 두꺼운 부분의 중심은 성형품의 표면에 비해 성형 냉각이 늦으므로 빨리 식어 수축이 일어나는 표면 쪽으로 수지가 잡아당겨진다. 성형 수축이 그 중심부에 집중된 결과로 중심부에 공동이 생긴다. 성형품 표면과 살 두께 중심부의 냉각 속도 차가 클수록 보이드가 발생하며, 늦은면 성형품 표면에 싱크 마크가 되어 나타난다.
대책
사출압력을 높임과 동시에 보압을 높게 한다
금형 온도를 높게 한다.
수지 온도를 낮게 한다.
사출 속도를 느리게 한다.
사출 유지시간을 길게 한다.
싱크마크
발생원인
싱크 마크는 성형품의 표면에 凹 모양으로 발생하는 것인데, 부피 수축량이 큰 살이 두꺼운 부분에 나타난다. 성형품이 냉각되는 과정에서 부피 수축이 발생하여, 중심부를 향해 수축하려는 하는 힘이 작용한다.
이때의 표면 스킨층의 강성과 수지가 수축하려고 하는 힘의 밸런스에서 스킨층이 약하면 성형품 중싱부로 끌어당겨져 성형품 표면에 나타나서 싱크마크가 된다. 강하면 성형품 중심부에 보이드가 발생한다. 살이 두꺼운 곳에서 스킨층의 강성과 수지가 수축하려고 하는 힘의 밸런스는 성형품 표면의 냉각 속도에 관계되는데 냉각 속도가 빠르면 보이드, 느리면 싱크마크가 된다. 또 냉각 속도가 느릴수록 부피 수축량이 작아져서 싱크 마크는 작아진다.
대책
사출압력을 높게 한다
일반적으로 금형 온도를 낮게 한다
사출 유지시간을 길게 잡는다.
수지 온도를 낮게 한다.
사출 속도를 느리게 한다.
쿠션량을 확보한다.
수지의 역류를 체크한다.
냉각 속도가 균일하게 되도록 금형을 검토한다.
사출 압축을 검토한다.
성형품 형상을 변경한다.
숏 샷
성형품의 일부가 충전 부족 때문에 미성형이 발생하는 현상을 말한다. 충전 중의 금형온도, 수지 온도, 사출 속도, 사출 압력 등의 영향을 받아 수지의 점성이 높아져서 유동이 정지하는 현상으로 압력, 속도를 증가해도 숏 샷이 된다.
전체적으로 숏샷이 발생하는 경우
발생원인
점성이 높아져서 숏샷이 발생한다
대책
금형 온도를 높게한다
수지 온도를 높게한다
사출 속도를 빠르게 한다
보압을 높게한다
사출 유지 시간을 길게 한다
성형품의 일부에 숏 샷이 발생하는 경우
발생원인
금형의 에어가 빠지지 않아 숏 샷이 발생한다
대책
사출 충전 완료 직전에 속도를 늦춘다
금형에 에어 벤트를 설치한다
성형품이 편육되어 있지 않은지 조사한다.
게이트의 위치를 검토한다.
버(플래시), 오버 팩(과충전)
성형품 전체에 버가 발생하는 경우
발생원인
형체력과 투영 면적과의 관계에서 형체력이 부족하면 금형이 열려 버가 발생한다
대책
금형 온도를 높게 한다
수지 온도를 높게 한다
사출 속도를 빠르게 한다
성형품의 95% 정도를 사출한 다음 보압으로 변환해서 압력을 낮게 한다
형체력이 한 랭크 큰 성형기로 바꾼다
성형품 일부에 버가 발생하는 경우
발생원인
금형 P.L의 맞춤 불량에 의한 버가 발생한다
형 버로 되어있는 것 때문에 버가 발생한다
금형이나 몰드 플레이트의 평행도가 나쁘고, 또 강도 및 강성이 부족한 것 때문에 버가 발생한다
대책
금형의 수정이나 형체력이 한 랭크 큰 성형기로 바꾼다
금형이 맞닿는 면의 면 압을 올리는 것도 검토한다
금형이 변형하지 않도록 강도를 높이는 것도 검토한다
성형 조건적으로 성형품 전에체 발생하는 경우와 마찬가지의 대책을 한다.
과충전
캐비티 내에 과충전된 현상으로 형을 없을 없게 되거나 이젝트 불량이나 크랙 등이 발생한다.
키워드에 대한 정보 사출 불량 종류
다음은 Bing에서 사출 불량 종류 주제에 대한 검색 결과입니다. 필요한 경우 더 읽을 수 있습니다.
이 기사는 인터넷의 다양한 출처에서 편집되었습니다. 이 기사가 유용했기를 바랍니다. 이 기사가 유용하다고 생각되면 공유하십시오. 매우 감사합니다!
사람들이 주제에 대해 자주 검색하는 키워드 #시험사출 #불량종류 #불량별 사출대처법 #사출 노하우 불량 유형별 대처 방법!!!
- 동영상
- 공유
- 카메라폰
- 동영상폰
- 무료
- 올리기
#시험사출 ##불량종류 ##불량별 #사출대처법 ##사출 #노하우 #불량 #유형별 #대처 #방법!!!
YouTube에서 사출 불량 종류 주제의 다른 동영상 보기
주제에 대한 기사를 시청해 주셔서 감사합니다 #시험사출 #불량종류 #불량별 사출대처법 #사출 노하우 불량 유형별 대처 방법!!! | 사출 불량 종류, 이 기사가 유용하다고 생각되면 공유하십시오, 매우 감사합니다.